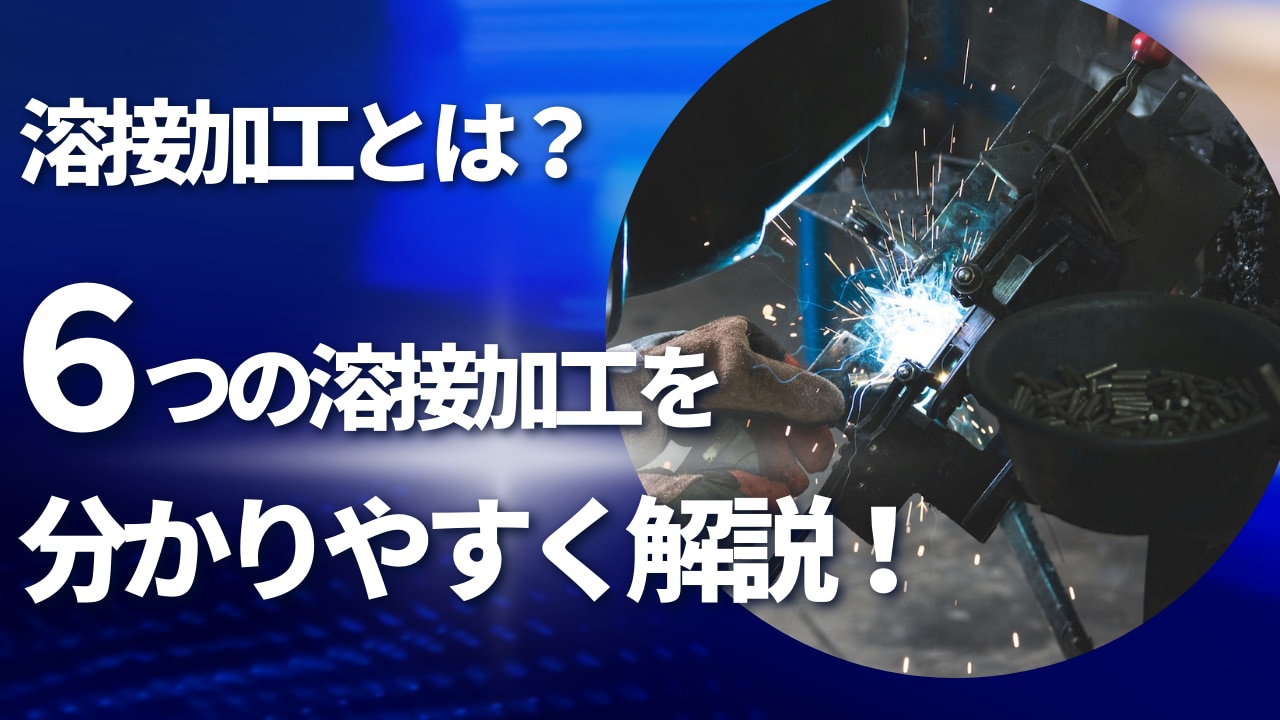
溶接加工とは?6つの溶接加工をわかりやすく解説
目次[非表示]
- 1.溶接加工の基礎知識
- 1.1.溶接の原理
- 1.2.溶接の種類(大きく分けて3種類:融接、圧接、ろう接)
- 1.3.溶接に使われる材料の種類
- 2.代表的な6つの溶接方法 小見出し:被覆アーク溶接
- 3. 溶接はどう進化する?溶接の未来
自動車、船舶、建築物、そして身近な家電製品に至るまで、その多くが溶接によって作られています。溶接とは、2つ以上の金属を高温で溶かし合わせ、一体化させる加工法です。
この技術は、その歴史は古く、人類が火を使い始めた頃から存在していたとされています。しかし、現代の溶接技術は、産業化によって、高度な機械と専門的な知識を必要とする複雑なものへと発展しました。
本記事では、溶接加工の基礎知識から、代表的な6つの溶接方法、そしてそれぞれのメリット・デメリットまでを詳しく解説していきます。溶接の種類によって、どのような金属に適しているのか、どのような特徴があるのかなど、具体的な事例を交えながらご紹介します。
溶接加工の基礎知識
溶接の原理
溶接の原理は、大きく分けて次の3つに分類されます。
- 熱による接合: 溶接部を加熱し、溶融状態にすることで原子同士を結合させます。この方法は、最も一般的な溶接方法であり、アーク溶接やガス溶接などがこれに当たります。
- 圧力による接合: 溶接部を加圧することで、原子同士を近接させ、冷間圧接や拡散接合といった方法で結合させます。
-
熱と圧力の複合による接合: 熱と圧力を同時に加えることで、より強固な接合を実現します。摩擦溶接などがこれに当たります。
溶接の種類や使用する材料によって、最適な接合方法が異なります。例えば、鉄鋼材料の溶接には熱による接合が一般的ですが、プラスチックの溶接には超音波溶接など、圧力による接合が用いられることもあります。
溶接の種類(大きく分けて3種類:融接、圧接、ろう接)
溶接は、接合方法によって大きく3種類に分類されます。
- 融接: 融接は、最も一般的な溶接方法で、熱によって材料を溶かし、溶融状態の金属を冷却することで接合する方法です。アーク溶接、ガス溶接、レーザー溶接などが代表的な融接方法。融接は、高い強度が求められる構造物や機械部品の接合に広く利用されています。
- 圧接: 圧接は、材料を加熱せずに、強い圧力を加えることで原子同士を結合させる方法です。冷間圧接、拡散接接などが代表的な圧接方法です。圧接は、熱による変形や変色が起こりやすい材料の接合や、電子部品の接合などに適しています。
- ろう接: ろう接は、溶点の低い金属(ろう)を溶かし、接合したい材料の間に流し込んで接合する方法です。ろうの種類によって、接合温度が異なり、様々な金属の接合に利用できます。ろう接は、気密性や耐食性が求められる部品の接合に適しています。
溶接に使われる材料の種類
溶接には、様々な種類の材料が使用されます。以下はその一例です。
・母材: 溶接の対象となる材料です。鉄鋼、ステンレス鋼、アルミニウム、銅など、様々な金属が母材として使用されます。
・溶加材: 溶接の際に、母材に添加する材料です。溶接棒、溶接ワイヤーなどが代表的な溶加材です。溶加材は、母材の種類や溶接方法に合わせて選択されます。
・フラックス: 溶接時に発生する酸化物を除去し、溶けやすくする物質です。溶接棒や溶接ワイヤーに含まれている場合もあります。
・保護ガス: 溶接部を酸化や窒素化から保護するために使用されるガスです。アルゴン、ヘリウム、二酸化炭素などが代表的な保護ガスです。
溶接材料の選択は、溶接の種類、母材の種類、溶接環境などによって使い分けられています。適切な材料を選択することで、高品質な溶接を実現することができます。
代表的な6つの溶接方法 小見出し:被覆アーク溶接
被覆アーク溶接は、最も古くから使用されている溶接方法の一つで、溶接棒と呼ばれる金属棒の表面に被覆剤を塗布したものを電極とし、アークを発生させて溶接する方法です。被覆剤は、溶接時に発生するガスを遮断し、溶融池を保護する役割を果たします。
メリット
- 設備が安価: 初期投資が少なく、導入しやすい。
- 汎用性が高い: 様々な金属に対応できる。
- 作業性が高い: 比較的簡単な操作で溶接できる。
デメリット
- 溶接速度が遅い: 自動化が難しいため、溶接速度が遅くなりがちです。
- 作業環境が悪化しやすい: 溶接時にスパッタが発生し、作業環境が悪化しやすい。
- 溶接品質が作業者の技量に左右される: 作業者の技量によって溶接品質が大きく左右される。
適した素材・用途
- 鉄鋼材料全般
- 厚板の溶接
- 構造物の製作
- 修繕
自動アーク溶接
自動アーク溶接は、溶接ワイヤーを連続的に供給しながらアークを発生させ、溶接を行う方法です。TIG溶接とMIG/MAG溶接が代表的な自動アーク溶接です。
メリット
- 生産性が高い: 溶接速度が速く、大量生産に適している。
- 溶接品質が安定: 作業者の技量に左右されにくい。
- 自動化が可能: 生産ラインへの導入が容易。
デメリット
- 設備投資が高い: 専用の溶接機が必要となり、初期投資がかかる。
- 作業範囲が限定される: ロボットの可動範囲内でしか作業できない。
適した素材・用途
- 薄板から厚板まで幅広く対応
- 大量の溶接が必要な場合
- 高い精度が求められる場合
TIG溶接
TIG溶接は、タングステン電極を使用してアークを発生させ、不活性ガスで溶接部を保護しながら溶接を行う方法です。
メリット
- 溶接品質が高い: 見た目を重視する製品に適している。
- 薄板の溶接に強い: 精密な溶接が必要な場合に適している。
デメリット
- 溶接速度が遅い: 自動化が難しく、溶接速度が遅い。
- 設備投資が高い: 専用の溶接機が必要となり、初期投資がかかる。
適した素材・用途
- ステンレス鋼
- アルミニウム
- 薄板
- 精密部品
MIG/MAG溶接
MIG/MAG溶接は、溶接ワイヤーを連続的に供給しながらアークを発生させ、不活性ガスまたは活性ガスで溶接部を保護する溶接方法です。
メリット
- 生産性が高い: 大量生産に適している。
- 自動化が可能: 生産ラインへの導入が容易。
- 汎用性が高い: 様々な金属に対応できる。
デメリット
- 溶接品質はTIG溶接に劣る: 溶接ビードがやや粗くなる場合がある。
- スパッタが発生しやすい: 作業環境が悪化しやすい。
適した素材・用途
- 鉄鋼材料
- ステンレス鋼
- アルミニウム
- 厚板の溶接
レーザー溶接
レーザー溶接は、高出力のレーザー光線を用いて金属を溶かし、接合する方法です。極めて高い精度で溶接が可能。電子部品などの微細な部品の溶接に適しています。
メリット
- 高精度: 精密な部品の製造に適している。
- 熱影響が小さい: 部品へのダメージが少ない。
- 自動化が可能: ロボットとの組み合わせにより、完全自動化が可能。
デメリット
- 高価な設備: レーザー装置が高価であり、初期投資がかかる。
- 専門的な知識が必要: 操作が難しく、専門的な知識が必要。
適した素材・用途
- 電子部品
- 自動車部品
- 医療機器
- 薄板の溶接
スポット溶接
スポット溶接は、2枚の金属板を重ねて、電極で強く圧着し、電流を流して接触面を加熱することで溶接する方法です。
メリット
- 生産性が高い: 大量生産に適している。
- 自動化が可能: 生産ラインへの導入が容易。
デメリット
- 溶接できる厚みが限られる: 厚板の溶接には不向き。
- 溶接部の強度が他の溶接方法に比べて低い場合がある。
適した素材・用途
- 自動車ボディ
- 家電製品
- 薄板の重ね合わせ
溶接はどう進化する?溶接の未来
近年では、溶接技術は目覚ましい発展を遂げています。ロボットによる自動化が進み、生産効率が大幅に向上しました。また、レーザー溶接など、高精度な溶接技術が開発され、電子部品や精密機器の製造にも活用されるようになりました。
溶接の未来は、ますます広がると期待されています。今後AIの活用により、溶接品質の向上や、最適な溶接条件の自動設定が可能になるでしょう。
また、新素材の開発に伴い、新たな溶接技術の開発も進み、より高度な製品の製造を可能にしていくでしょう。