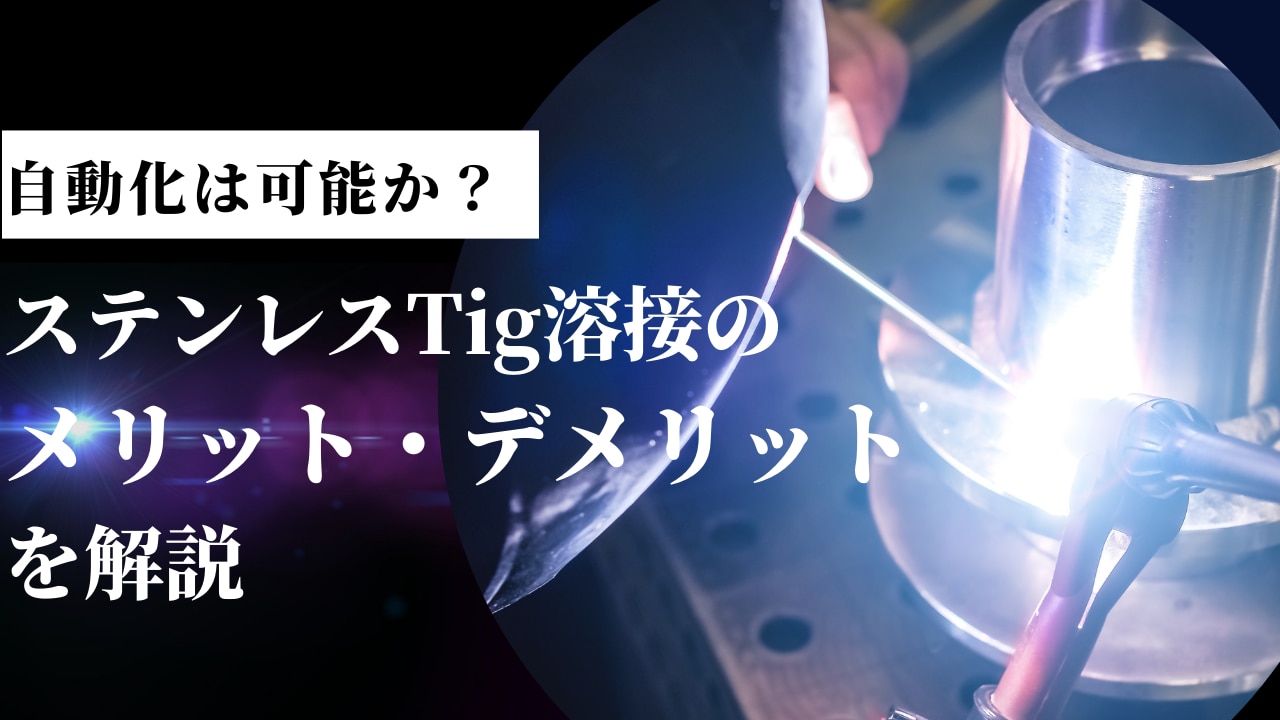
ステンレスTIG溶接のメリット・デメリットを解説 自動化は可能か?
TIG(Tungsten Inert Gas)溶接は、耐食性、延性、靭性に優れている溶接方法です。様々な金属でも使われていますが、ステンレスでも使われています。
この記事では、TIG溶接メリットとデメリットを詳しく説明していきます。
目次[非表示]
- 1.TIG溶接のメリットとは?
- 1.1. 溶接品質が高く、外観が美しい
- 1.2.薄物やステンレスなどの溶接加工が可能
- 1.3.火花が発生しないため安全性が高い
- 2.TIG溶接のデメリット
- 2.1.溶接範囲が狭い
- 2.2. 溶接する鋼材の間に隙間があると溶接しにくい
- 2.3.溶接速度が遅い
- 2.4. 溶接後の処理に時間がかかる
- 3. ステンレスTIG溶接の今後の課題
- 3.1. 自動化がまだまだ進みづらい
- 3.2.ステンレス鋼に対応していく必要がある
- 3.3.環境への配慮
- 3.4. 技術者の育成
- 4. まとめ
TIG溶接のメリットとは?
ステンレスは水に強いため、お風呂やキッチンのシンクなど、水を使う場所でよく使われます。水が漏れたり、空気が入ったりしないように、しっかりと密封できる溶接が必要です。そこでTIG溶接が使われます。
TIG溶接にはどんなメリットとデメリットがあるのでしょうか?まずはメリットを詳しく紹介していきます。
溶接品質が高く、外観が美しい
タングステン電極と保護ガスを用い、高い精密さで作業が行われるため、均一かつ耐食性に優れた溶接を実現できます。こうした高い品質は、特に外観の美しさや耐久性が求められる製品で使われています。
薄物やステンレスなどの溶接加工が可能
幅広い素材に対応できるのが、TIG溶接の強みです。高い精密を有し、薄い素材に対しても適切に熱を加え、安定して溶接することが可能です。
その結果、薄物の歪みや変質を最小限に抑えながら、高品質な溶接を実現できます。特に、外観や強度に厳しい要求がある製品において、ステンレスTIG溶接は頼りにされる方法となっています。
火花が発生しないため安全性が高い
TIG溶接は非常に制御された電弧を使用し、溶融プールを形成する際に火花が発生しにくいです。そのため、作業中に火花が飛び散る心配が少なくなり、作業環境が安全であるという利点があります。
特に、燃えやすい環境や可燃性ガスの近くでの作業において、ステンレスTIG溶接は高い安全性が評価されています。作業者の安全を確保し、作業現場のリスクを軽減するうえで欠かせないポイントです。
TIG溶接のデメリット
次にTIG溶接のデメリットをご紹介していきます。
溶接範囲が狭い
TIG溶接は通常、薄板や精密な部品に向いています。例えば、航空機や食品加工機器の製造などで使用されることがあります。
しかし、厚板や大型構造物の場合、TIG溶接は効率的でなく、時間がかかる傾向があります。さらに、高電流が必要なため、電源の制約や適切な作業環境が必要です。
これにより、大規模な製造プロセスや高い生産性が求められるプロジェクトでは、他の溶接法(例: MIG(金属活性ガス)溶接)がより適していることがあります。
TIG溶接は高い精度と制御が可能なため、要求水準の高い製品において優れた選択肢となりますが、目的の要件や材料の特性に応じて、他の溶接方法と組み合わせて使用することが重要です。
溶接する鋼材の間に隙間があると溶接しにくい
TIG溶接は高精度で細部の溶接に適していますが、隙間が広がると均一な溶接が難しくなります。隙間が生じると、材料の均一な溶解や溶接材の十分な供給が妨げられ、溶接部の剛性や密閉性に影響を与える可能性があるからです。
したがって、事前に材料の適切な合わせや正確な加工が必要です。また、溶接時には隙間に十分な溶接材を流して、均等な接合をする技術が求められます。これにより、隙間が生じにくく、強度や品質が向上します。
溶接速度が遅い
TIG溶接は高精度で美しい仕上がりが得られる反面、作業速度が他の溶接法に比べて遅い傾向があります。これは、TIG溶接が手作業になるためであり、高い技術と慎重な作業が必要だからです。
高い精密性を追求するTIG溶接では、ポイントを合わせた作業が求められ、溶接速度を上げるのは簡単ではありません。また、高い品質を維持するためには、適切な電流設定や溶接材料の供給量を調整する必要があり、知識と経験が求められます。
このデメリットから、工場のラインで行われる大量生産の現場で導入が難しいと言われる理由がわかるのではないでしょうか?
一方で、高い品質が求められる特定の用途や精密な部品製造においては、制御性や仕上がりの綺麗さなど、TIG溶接が求められる理由になっています。
溶接後の処理に時間がかかる
ステンレス鋼の溶接では、酸化皮膜や色調の変化が発生しやすいため、これらを取り除いて均一な仕上がりを実現するために手間がかかります。また、見た目への要求が高い場合、細部への配慮が必要で、これが時間を必要する原因になります。
処理には、研磨や研磨剤の選定、表面仕上げなどが含まれていますが、品質を維持するためには欠かせない工程となります。
つまり、TIG溶接は表面上の綺麗さを追求するなら適切ですが、その反面、手間暇がかかることを理解して、製造工程やプロジェクトのスケジュールを組む必要が出てきます。
小見出し:熟練度によって仕上がりが変わる
TIG溶接は高精度な作業というのは、ここまででわかっていただけたのではないでしょうか?溶接者の技術や手腕がその品質に直結します。正確な電流制御やトーチの操作は職人技であり、十分にマスターするには経験と訓練が必要です。たった1ヶ月で習得できるわけではありません。
不慣れな担当者が行なうと、均一な溶接が難しく、欠陥や不完全な仕上がりとなり、クレームにつながります。特に薄板や複雑な形状の部品では、微細な操作が求められ、熟練の溶接者が担当することが多いです。
一方で、熟練の溶接者は減少傾向にあり、職人不足が問題となってきています。
ステンレスTIG溶接の今後の課題
ステンレスのTIG溶接の今後の課題には、主に以下の点が挙げられます。
自動化がまだまだ進みづらい
TIG溶接は手作業に依存しているのはわかっていただけましたよね。高い技術と経験が必要だからこそ、日本らしい手仕事として評価されています。
一方、自動化が進む他の溶接法に比べて生産性が制約されているのが課題です。
ただ、自動化に挑戦する企業も存在しており、全く自動化が難しいというわけではありません。例えば、リンクウィズは板金TIG溶接の自動化のパッケージを販売しています。職人への依存度が高かった板金TIG溶接を「誰にでもできる作業」へと変革しています。
「L-ROBOT 板金溶接パッケージ」の詳細はこちら
https://bankin-yousetsu.com/
ステンレス鋼に対応していく必要がある
次に、新しい合金の開発とその溶接技術への適用が求められます。進化する需要に対応するためには、耐腐食性や耐熱性が向上した新しいステンレス鋼の開発が進む中で、それらに適した溶接技術の研究や実用化が必要とされてきます。
環境への配慮
環境への配慮も課題となっています。溶接プロセスにおけるエネルギーの効率化や廃棄物の削減、環境への影響の最小化など、持続可能性を考慮した改善が求められます。
技術者の育成
最後に、技術者の育成が不可欠です。TIG溶接は高度な技術と経験を要するため、質の高い技術者の育成が欠かせません。しかし、実際は若い人が溶接の仕事に就職しないなど、そもそもの人材不足の問題を抱えている業界です。ロボットによる自動化など、人材に依存しすぎない経営が求められています。
まとめ
ステンレスのTIG溶接は綺麗な仕上がりや精密さが魅力ですが、熟練の技術が必要であり、溶接速度が遅いというデメリットがあります。
将来に向けては、人材不足の懸念などがあり、早急な自動化対策が求められています。持続可能な生産現場を維持していくためにも、現場の効率化や簡素化などを進めていく必要があるでしょう。